A
AndrewB
Morning Gents,
I hope that you can help me with this problem. I am not an electrician - I just know enough to be dangerous.
I recently bought this beautiful beast :
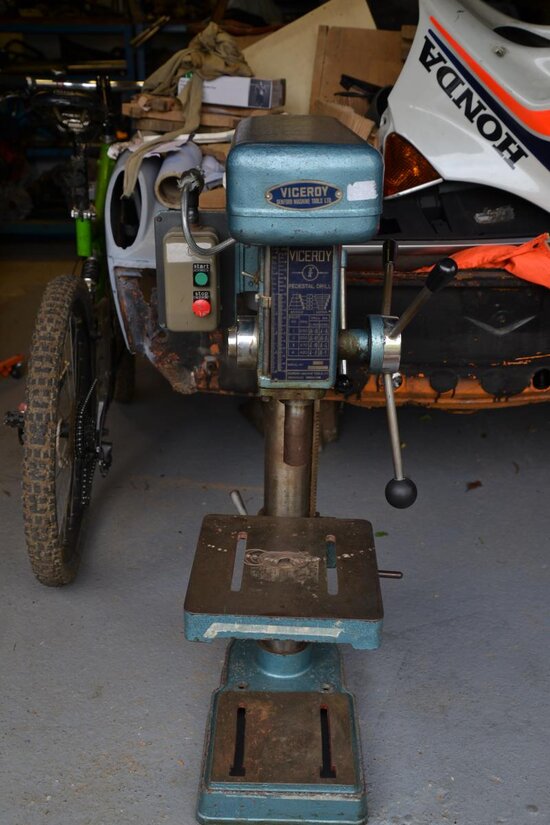
It's a Denford tools Viceroy pillar drill from the 60s or maybe even the 50s. Nice and cheap with one catch - it had a non original 3 phase motor with some strange rating on the data plate which baffled both the bloke I bought it from and my friendly electrical expert. Therefore - much as I would have liked speed control - I went the easy route and bought an ancient AEI single phase motor with the necessary – and hard to find - 5/16” shaft for a tenner.
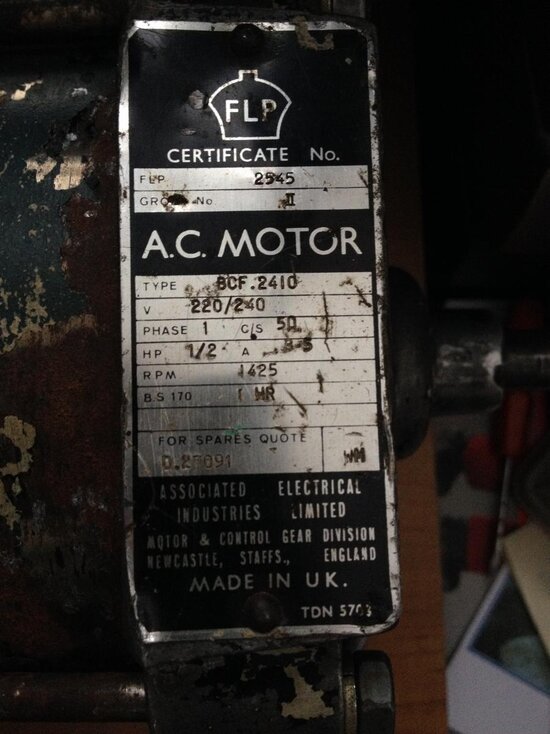
Having played with the internal shimming, fabbed up a new bracket and swapped the contactor I now have a lovely working quality pillar drill for under £80. I like a bargain.
However - it goes the wrong bloody way round and as I want to make holes not fill them I'm a bit puzzled.
I swapped the L and N on the motor - no difference. A quick google tells me it must be a split phase motor - never heard of them.
So chaps - what do I (can I ?) do ?
An idler pulley is an option but a lot of faff. I can't afford any more major expense on another motor or going the 3 phase route - I want to work with what I've got.
If I open up the motor (been in there already for a once over and to free it off) can I swap the orientation of the central outer section (don't know the correct term) whilst leaving the armature and end caps in the same relative positions. I'm guessing there will be a couple of wires to swap as well although as the photo shows - the 2 supply cables are connected to the centre 'barrel' NOT the bottom end cap.
Logically - when these motors were built - they must have been designed so that they could be provided with either rotation so as to suit different applications ?
I'm sure it's not quite that simple but any advice would be appreciated.
Cheers
Andrew
I hope that you can help me with this problem. I am not an electrician - I just know enough to be dangerous.
I recently bought this beautiful beast :
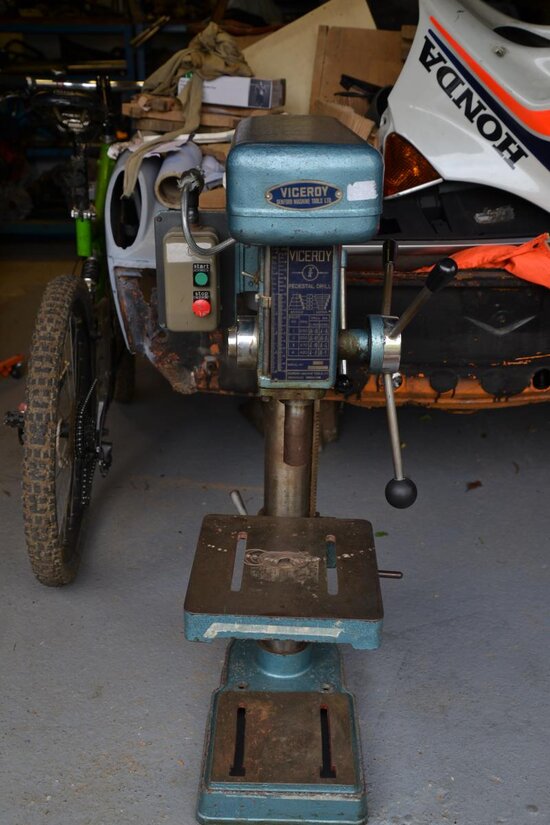
It's a Denford tools Viceroy pillar drill from the 60s or maybe even the 50s. Nice and cheap with one catch - it had a non original 3 phase motor with some strange rating on the data plate which baffled both the bloke I bought it from and my friendly electrical expert. Therefore - much as I would have liked speed control - I went the easy route and bought an ancient AEI single phase motor with the necessary – and hard to find - 5/16” shaft for a tenner.
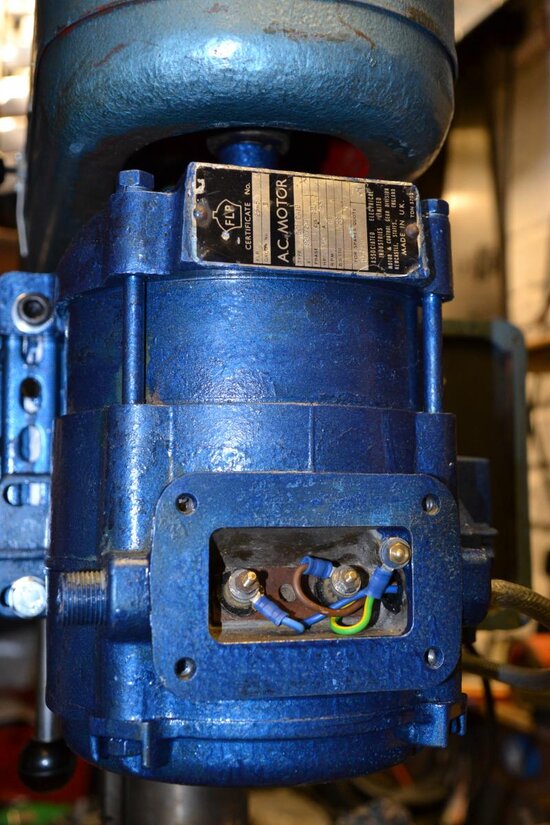
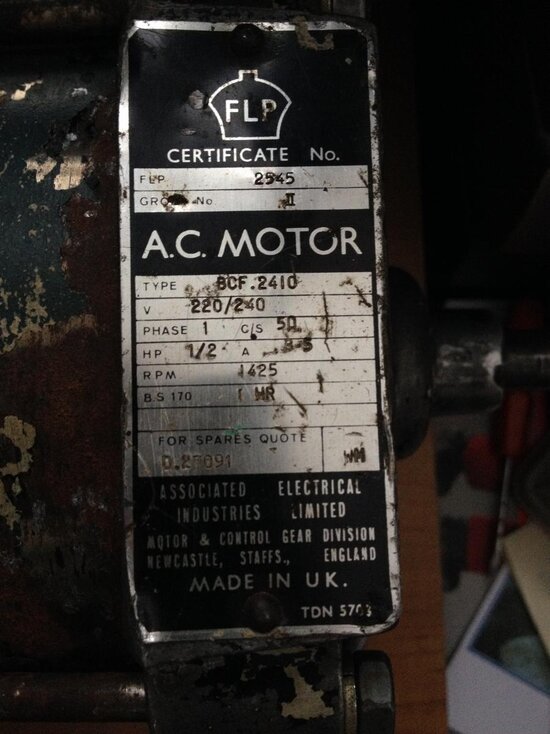
Having played with the internal shimming, fabbed up a new bracket and swapped the contactor I now have a lovely working quality pillar drill for under £80. I like a bargain.
However - it goes the wrong bloody way round and as I want to make holes not fill them I'm a bit puzzled.
I swapped the L and N on the motor - no difference. A quick google tells me it must be a split phase motor - never heard of them.
So chaps - what do I (can I ?) do ?
An idler pulley is an option but a lot of faff. I can't afford any more major expense on another motor or going the 3 phase route - I want to work with what I've got.
If I open up the motor (been in there already for a once over and to free it off) can I swap the orientation of the central outer section (don't know the correct term) whilst leaving the armature and end caps in the same relative positions. I'm guessing there will be a couple of wires to swap as well although as the photo shows - the 2 supply cables are connected to the centre 'barrel' NOT the bottom end cap.
Logically - when these motors were built - they must have been designed so that they could be provided with either rotation so as to suit different applications ?
I'm sure it's not quite that simple but any advice would be appreciated.
Cheers
Andrew
Last edited by a moderator: