J
jjnr78
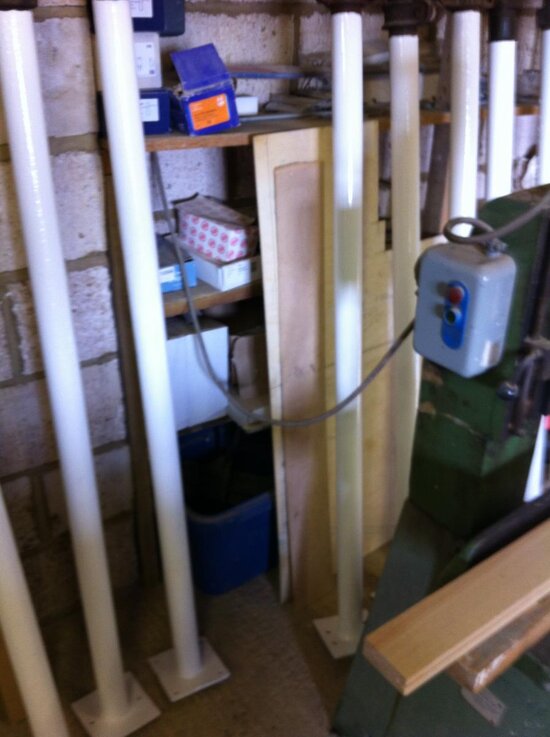
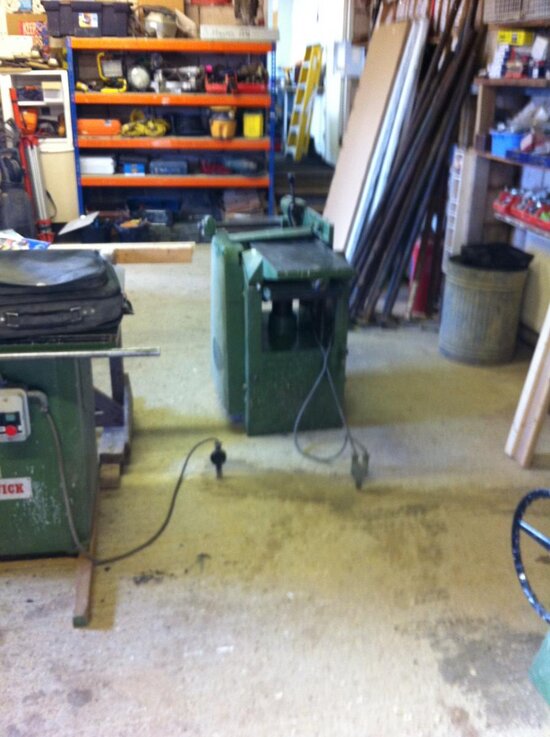
I attended an inspection of an office and workshop last week. There were quite a few issues, but I was intrigued by the issues depcited in the photos. They had 4, 3phase machines (saw, drill, grinder, plane) which were wired into only 2 isolators (and 2 circuit breakers). they did have emergency stop buttons on all but the grinder. 2 machines that were in the middle of work shop were wired from the isolators using steel conduit finished with beezer boxes that just stuck out from the floor! They then had an early style kopex (stell braided flex) which is no freyed at the box and machine end for the connection. One had a loop of braided flex from the wall to the machine and the users had stood acros either side that could have fallen and pulled the connection clean out. In old money I would class this as a code 2, do you agree? How would you remedy the issue? I've thought about building a more substantial structure and mounting individual isolator at a high level with less strain and trip hazard!:confused5: